Why buy expensive stainless steel flood vents...Orders ship within 2 business days
​
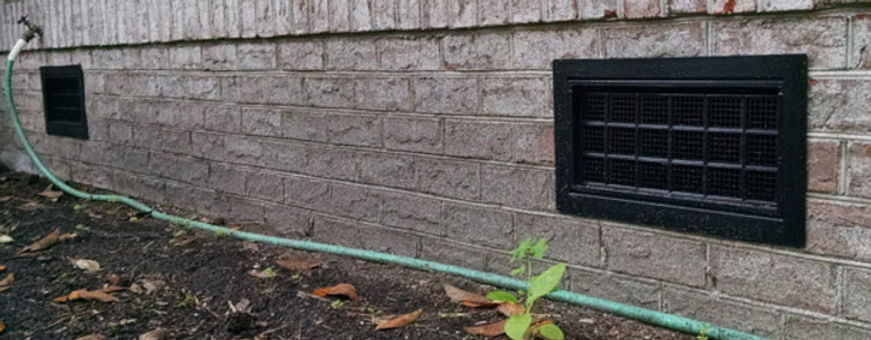
FAQ
ANSWERS? WE'VE GOT THEM.
Here are the questions we are most frequently being asked:
GENERAL
What is a Flood Vent?
Flood vents are permanent openings in a wall designed to protect houses and buildings in floodplains by allowing the unobstructed passage of water, automatically, in both directions in to or out of the building’s interior, thus reducing water pressure buildup that can destroy walls and foundations.
Why and When are Flood Vents required?
Flood vents may substantially reduce the destruction and damage to a structure’s foundation during floods. Flood vents relieve hydrostatic pressure on the foundation walls to help prevent/minimize structural damage to the building.
The NFIP Regulations and Building Codes require that any residential or even commercial building constructed in Flood Zone Type A have the lowest floor, including basements, elevated to or above the Base Flood Elevation (BFE). Enclosed areas are permitted under elevated buildings provided that they meet certain use restrictions and construction requirements such as the installation of flood vents to allow for the automatic entry and exit of flood waters.
Flood vents may substantially reduce the destruction and damage to a structure during certain flood events. Proper flood venting may even qualify the owner for reduced flood insurance premiums. Check with an insurance to see if adding automatic, engineered flood vents like Flood Flaps will reduce the premium on your existing flood insurance policy.
What is the difference between Wet Floodproofing and Dry Floodproofing?
Wet floodproofing allows flood waters to enter the enclosed areas of a structure. In contrast, dry floodproofing prevents the entry of flood waters.
The benefit of wet floodproofing is that if flood waters are allowed to enter the enclosed areas of the structure and to quickly reach the same level as the flood waters outside, the effects of hydrostatic pressure, including buoyancy, are greatly reduced. As a result, the loads imposed on the structure during a flood, and therefore the likelihood of structural damage, may be greatly reduced.
Is my property in a flood zone?
Zoning can be determined by viewing FEMA’s Flood Map Service Center (DFIRM) or FreeFlood.com.
What is the Base Flood Elevation (BFE)?
The Base Flood Elevation (BFE) is the regulatory requirement for the elevation or floodproofing of structures. The relationship between the BFE and a structure's elevation determines the flood insurance premium. The computed elevation to which floodwater is anticipated to rise during the base flood. BFEs are shown on Flood Insurance Rate Maps (FIRMs) and on the flood profiles.
What is a Special Flood Hazard Area (SFHA)?
The land area covered by the floodwaters of the base flood is the Special Flood Hazard Area (SFHA) on NFIP maps. The SFHA is the area where the NFIP's floodplain management regulations must be enforced and the area where the mandatory purchase of flood insurance applies. The SFHA includes Zones A, AO, AH, A1-30, AE, A99, AR, AR/A1-30, AR/AE, AR/AO, AR/AH, AR/A, VO, V1-30, VE, and V.
What is Freeboard?
Freeboard is a factor of safety usually expressed in feet above a flood level for purposes of floodplain management. "Freeboard" tends to compensate for the many unknown factors that could contribute to flood heights greater than the height calculated for a selected size flood and floodway conditions, such as wave action, bridge openings, and the hydrological effect of urbanization of the watershed. Freeboard is not required by NFIP standards, but communities are encouraged to adopt at least a one-foot freeboard to account for the one-foot rise built into the concept of designating a floodway and the encroachment requirements where floodways have not been designated. Freeboard results in significantly lower flood insurance rates due to lower flood risk.
CODES
FEMA, NFIP, and Building Code requirements
• Regulations require that enclosed areas surrounded by solid walls that extend below the BFE have flood openings.
o Several examples of enclosures that require openings are described below:
ï‚§ Solid perimeter foundation walls (crawlspaces or under-floor spaces)
ï‚§ Solid perimeter foundation walls (below-grade crawlspaces)
ï‚§ Solid perimeter foundation walls (with full-height under-floor spaces)
ï‚§ Garages attached to elevated buildings
ï‚§ Enclosed areas under buildings elevated on open foundations in A zones
ï‚§ Enclosed areas with breakaway walls under buildings elevated on open foundations in A zones
ï‚§ Solid perimeter foundation walls on which manufactured homes are installed
ï‚§ Accessory structures (detached garages and storage sheds)
• Each enclosed area is required to have a minimum of two openings on exterior walls to allow floodwaters to enter directly. In order to meet the requirement, the openings must be located so that the portion of the opening intended to allow for inflow and outflow is below the BFE.
o Openings that are entirely above the BFE (or any portion of an opening that is above the BFE) will not serve the intended purpose during base flood conditions and thus are not counted towards the compliance with the flood opening requirements.
• The openings should be installed on at least two sides of each enclosed area to decrease the chances that all openings could be blocked with floating debris and to allow for more even filling by floodwater and draining of the enclosed area.
• The bottom of each opening is to be located no higher than 1 foot above the grade that is immediately under each opening.
o Finished exterior grade - Care should be taken when placing backfill, topsoil, and landscaping materials around the outside of enclosures, especially solid perimeter foundation walls. If the finished exterior grade is higher than the interior grade on all sides of the building, then the enclosed area becomes a basement as defined by the NFIP.
o Final interior grade - The trench that is excavated to construct footings and foundation walls must be backfilled completely, otherwise a basement is created. If the interior grade is higher than the exterior grade, the openings are to be no higher than 1-foot above the interior grade.
• Any screens, grates, grilles, fixed louvers, or other covers or devices must not block or impede the automatic flow of floodwaters into and out of the enclosed area.
• Stacked vent devices may be installed. If the BFE does not reach the top of the opening, only the portion that is below the BFE will count as contributing to the required net open area.
FLOOD FLAPS PRODUCT FEATURES
How do Flood Flaps flood vents provide 220 square feet of flood coverage?
All of Flood Flaps flood vent products are automatic, engineered flood openings. Our products have been evaluated and certified by the International Code Council’s Evaluation Service (ICC-ES) to provide 220 square feet of flood coverage. No other ICC evaluated flood vent can match our coverage area.
A non-engineered opening is one that is simply measured by calculating the opening in the vent itself. FEMA Guidelines (as outlined in Technical Bulletin 1-08) do state that a non-engineered flood vent solution must (among other requirements) provide 1 sq. in. of opening per 1 sq. ft. of space vented. This guideline only applies to non-engineered openings, like traditional air vents.
How do your flood vents work?
In non-flood situations, the grill and rubber flaps (if applicable) remain in their secure position to operate as designed. During a flood, the hydrostatic pressure of rising flood waters will disengage the grill and rubber flaps to allow flood waters and debris to pass in either direction. Flood water can enter or exit an enclosed area through a Flood Flaps flood vent.
Our flood vents do not require any fancy bobbers, floats or other devices to allow flood water to enter or exit though the flood opening. Our simple design only requires water pressure to disengage our components.
How does a Sealed Series model differ from a Multi-Purpose model?
Conceptually it’s simple: Do you want air circulation or not?
Flood Flaps Sealed Series models are perfect for structures located in floodplains that desire conditioned space or an encapsulated crawlspaces. These models use two (2) rubber flaps to keep air from passing through the flood opening in non-flood situations, 365 days a year. In the case of a flood, the rubber flaps will give to the pressure of flood water and allow water to enter or exit the flood opening. Energy efficient flood vents such as Flood Flaps Sealed Series models are even more important as states are adopting and enforcing the 2015 International Energy Conservation Code. Flood Flaps Sealed Series models provide a tight seal (watch a video and see for yourself) to keep enclosures protected from exterior climate air and insects.
Flood Flaps Multi-Purpose models are also FEMA compliant flood vents certified to provide flood protection and air ventilation (37 square inches). These models are perfectly designed for an enclosure or crawlspace in a flood plain that desires natural air while still providing efficient flood relief when necessary. The patented grill remains closed and secure until forced open by flood waters, allowing water to enter or exit the enclosed area.
Do they come in different colors?
Our flood vents are offered in black, gray and white. Custom color options are available.
Do they come in custom sizes?
Flood Flaps flood vents can be stacked vertically or grouped horizontally, to fit the dimensions of most openings. For larger applications, including commercial settings, we can provide larger, custom arrays that don’t require special mounting accessories. Flood Flaps is happy to create a customized flood vent based on dimensions provided and ship as a single unit.
Do your vents require annual preventative maintenance like other steel vents?
Flood Flaps flood vents do not require any preventative maintenance at any time. No rinsing, no lubricating. Simply install and let them operate as designed.
Do your vents keep out rodents and vermin?
Flood Flaps uses anodized aluminum, imbedded in an engineered plastic grill, to prevent rodents and vermin from passing through the flood opening. In non-flood situations, the grill remains secured by six (6) raised tabs and takes roughly 15 pounds of pressure to disengage.
Do you have a vent that keeps air, moisture, humidity, insects, dust and/or pollen from passing through the opening?
Flood Flaps Sealed Series models use two (2) rubber flaps to keep air, moisture, humidity, insects, dust and pollen from passing through the flood opening in non-flood situations, 365 days a year. No other ICC evaluated flood vent product can match its superior performance.
How can I finish the appearance of the flood opening on the inside?
Flood Flaps offers an interior trim flange to provide a clean, handsome, finished look on the interior. Our flood vent products also come in three different depths to accommodate most installation scenarios. This eliminates the need to purchase extension sleeves that can be expensive and difficult to install.
CERTIFICATION
What is the difference between Engineered Openings and Non-engineered Openings?
Engineered openings, like Flood Flaps, are specifically designed and tested as flood vents, and are given a flood coverage rating based on performance, as meeting the required performance and design requirements as outlined by FEMA, NFIP and Building Codes. Flood Flaps flood vents are ICC-ES evaluated and certified to provide 220 square feet of flood protection per flood vent.
Non-engineered openings have not gone through any of the required evaluating or testing to qualify as an engineered flood vent. Typically non-engineered openings are used for air venting purposes only. Therefore, they are rated at the assumptive method of 1 net sq. inch of opening per 1 foot of enclosed area. Click here for FEMA Technical Bulletin 1-Openings in Foundation Walls and Walls of Enclosures.
What documentation or certification is required for an Engineered Openings?
Engineered openings or devices may be accepted by local officials as an alternative to non-engineered openings provided the designs are certified. The certification may take the form of the individual certification or it can be an Evaluation Report issued by the ICC-ES.
A copy of the individual certification or the Evaluation Report is required to be kept in the community’s permanent permit files, along with inspection reports. The documentation can be submitted as part of the permit application and design drawings, or submitted separately. Owners should retain the certification or a copy of the Evaluation Report to submit along with applications for NFIP flood insurance.
For non-ICC evaluated flood vents, the original certification of the engineered openings must include the following:
• design professional’s name, title, address, signature, type of license, license number, the State in which the license was issued,
• and the signature and applied seal of the certifying registered design professional
• the certification shall identify the building in which the engineered openings will be installed
• A statement certifying that the openings are designed to automatically equalize hydrostatic flood loads on exterior walls by allowing the automatic entry and exit of floodwaters in accordance with the Engineered openings design requirements
• Description of the range of flood characteristics tested or computed for which the certification is valid, such as rates of rise and fall of floodwaters
• Description of the installation requirements or limitations that, if not followed, will void the certification
What are some examples of Non-Acceptable Flood Openings as defined by FEMA?
• Standard foundation air ventilation devices that can be closed manually, because they do not allow for the automatic entry and exit of floodwaters unless they are permanently disabled (broken) in the open position.
• Standard foundation air ventilation devices that have detachable solid covers that are intended to be manually installed over the opening in cold weather, because they do not allow for the automatic entry and exit of floodwaters when the cover is in place.
• Standard foundation air ventilation devices that are designed to open and close based on temperature (unless they also are designed to allow for the automatic entry and exit of floodwaters).
• Windows below the BFE, because the automatic entry and exit of floodwaters cannot be satisfied by the expectation that windows will break under rising floodwaters.
• Garage doors without openings installed in them, because human intervention is required to open the doors when flooding is expected. Gaps between the garage door and the doorjamb or walls do not count towards the net open area requirement.
• Standard exterior doors without openings installed in them.
For further information see the Unacceptable Measures Section on Page 19 of FEMA TB 1-08.
What is the International Code Council (ICC)?
The International Code Council, a membership association dedicated to building safety and fire prevention, develops the codes used to construct residential and commercial buildings, including homes and schools. Most U.S. cities, counties and states that adopt codes choose the International Codes developed by the International Code Council.
Flood Flaps ICC Certification Evaluation Service Report (ESR-3560) states that one 16" x 8" Flood Flaps flood vent is certified to provide 220 sq. ft. of flood protection. ICC Evaluation Reports should be attached to the Elevation Certificate.